‘Lean Manufacturing’ ลดความสูญเปล่า เพิ่มความยั่งยืน
การผลิตแบบลีน (lean manufacturing) มีจุดเริ่มต้นมาจากผู้ผลิตรถยนต์แบรนด์โตโยต้า ประเทศญี่ปุ่น ต้องพาโรงงานฝ่าฟันวิกฤตหลังสงครามโลกครั้งที่ 2 ซึ่งเป็นช่วงขาดแคลนทั้งคน เงิน และพื้นที่ รวมถึงต้องเผชิญกับปัญหากลุ่มเป้าหมายมีความต้องการรถยนต์ลดลงแต่มีความต้องการรูปแบบของยานยนต์ที่มากยิ่งขึ้น ทำให้ต้องปรับเปลี่ยนกระบวนการผลิตเพื่อลดความสูญเปล่าให้ได้มากที่สุด จนเกิดเป็นแนวทาง ‘Toyota Production System (TPS)’ ที่ประสบความสำเร็จอย่างมาก หลังจากนั้นคณะอาจารย์และนักศึกษาจาก Massachusetts Institute of Technology (MIT) สหรัฐอเมริกา จึงได้ช่วยกันถอดแนวทางความสำเร็จของ TPS โดยขยายแนวคิดและเพิ่มเติมเครื่องมือสำหรับลดความสูญเปล่า ก่อนให้ชื่อแนวทางที่พัฒนาต่อยอดว่า ‘lean manufacturing’ ดังที่มีการใช้งานแพร่หลายในปัจจุบัน
กระทรวงการอุดมศึกษา วิทยาศาสตร์ วิจัยและนวัตกรรม (อว.) โดยศูนย์เทคโนโลยีอิเล็กทรอนิกส์และคอมพิวเตอร์แห่งชาติ (เนคเทค) สำนักงานพัฒนาวิทยาศาสตร์และเทคโนโลยีแห่งชาติ (สวทช.) ร่วมกับคณะบริหารธุรกิจ สถาบันเทคโนโลยีไทย-ญี่ปุ่น (TNI) พัฒนา ‘Digital lean manufacturing coaching program’ สำหรับช่วยเหลือผู้ประกอบการไทยในการนำหลักคิด lean manufacturing ไปใช้ปรับปรุงกระบวนการผลิตอย่างยั่งยืน
ความสูญเปล่า 7 ประการ ยิ่งรู้เร็ว ยิ่งลดความเสียหาย
โดยทั่วไปความสูญเปล่าของโรงงานมักเกิดขึ้นจากการขาดการบริหารจัดการที่เป็นระบบและละเอียด ถี่ถ้วน การขาดเทคโนโลยีที่เหมาะสมในการดำเนินงาน การขาดความเชี่ยวชาญ และการขาดวัฒนธรรมองค์กรที่มุ่งให้ทุกคนมีส่วนในการลดความสูญเปล่า
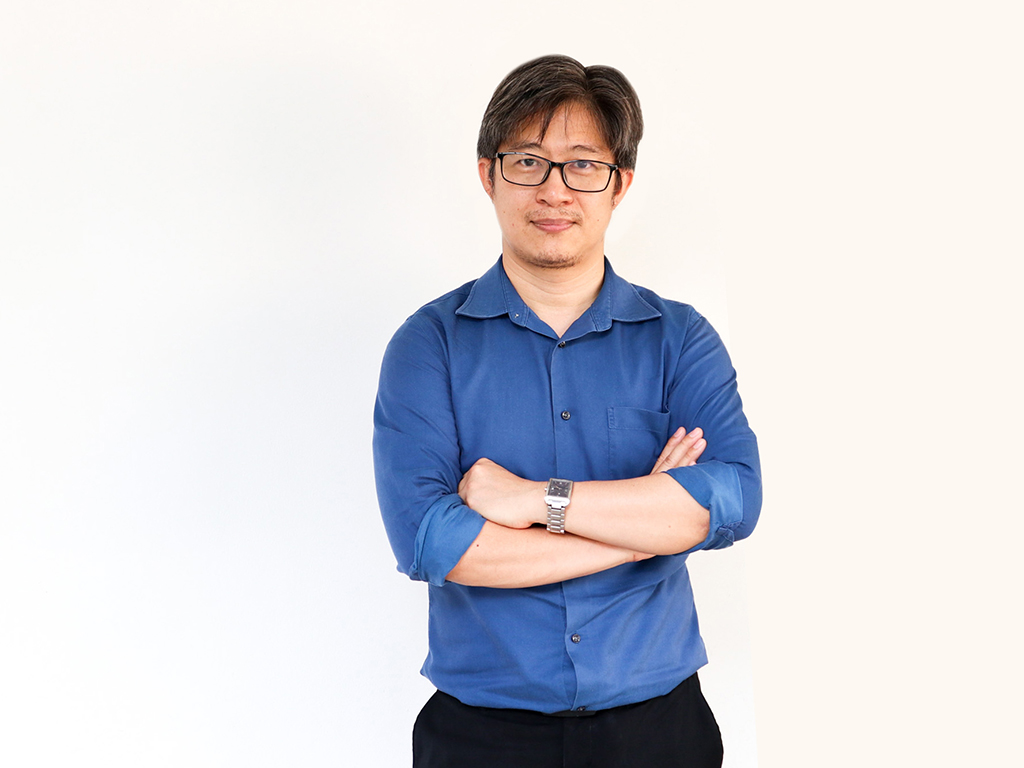
ดร.ธนกร ตันธนวัฒน์ ทีมระบบไซเบอร์-กายภาพ (CPS) เนคเทค สวทช. อธิบายว่า ความสูญเปล่า 7 ด้านที่เป็นปัญหาร่วมของโรงงานส่วนใหญ่ คือ 1) การผลิตมากเกิน 2) การมีสินค้าคงคลัง 3) การขนย้ายวัสดุ 4) การเคลื่อนไหวของคนหรือเครื่องจักร 5) การทำงานซ้ำซ้อน 6) การรอคอย 7) การมีของเสีย (ดูรายละเอียดเกี่ยวกับความสูญเปล่าทั้ง 7 ด้านได้จากภาพประกอบ) ซึ่งทั้งหมดนี้ล้วนส่งผลให้เกิดการสิ้นเปลืองทั้งเวลา ค่าแรง ค่าเครื่องจักร ค่าซ่อมบำรุง และค่าพลังงานที่เกินความจำเป็น นอกจากนี้ยังทำให้เสียโอกาสในการรับงานเพิ่ม และอาจร้ายแรงถึงขั้นเสียความน่าเชื่อถือทางธุรกิจได้ด้วย
ทั้งนี้แม้หลักการและแนวคิดการลดความสูญเปล่าจะดูเป็นเรื่องที่เข้าใจง่าย แต่ก็มักถูกมองข้ามหรือมองไม่เห็น เป็นผลมาจากผู้บริหารและพนักงานต่างคุ้นชินกับสภาพการทำงานที่เป็นอยู่ นอกจากนี้หลายครั้งเมื่อมีกระแสของเทคโนโลยีขั้นสูงเข้ามาสร้างการเปลี่ยนแปลง (disrupt) ในอุตสาหกรรมต่าง ๆ ก็อาจทำให้หลายองค์กรรีบขวนขวายนำเทคโนโลยีเหล่านั้นมาใช้งานจนไม่ได้คิดให้ถี่ถ้วนว่าเหมาะกับบริบทขององค์กรอย่างแท้จริงหรือไม่ ทำให้เกิดความสูญเปล่าโดยไม่จำเป็นเพิ่มขึ้นมาอีกด้วย ดังนั้นแล้วแต่ละองค์กรจำเป็นอย่างยิ่งที่จะต้องตรวจสอบความสูญเปล่าภายในโรงงานอยู่เสมอ เพื่อให้เท่าทันต่อสถานการณ์ และลดความสูญเปล่าให้ได้มากที่สุด
ดร.ธนกร อธิบายว่า จากประสบการณ์การทำงานร่วมกับผู้ประกอบการในอุตสาหกรรมต่าง ๆ ทั้งขนาดเล็ก ขนาดกลาง ไปถึงขนาดใหญ่ ทำให้ทราบว่าขั้นตอนสำคัญที่สุดของการปรับปรุงกระบวนการผลิตตามหลักการ Lean manufacturing คือ การระบุต้นตอและจัดลำดับความสำคัญของปัญหา ศูนย์นวัตกรรมการผลิตยั่งยืน (SMC) เนคเทค สวทช. จึงร่วมกับคณะบริหารธุรกิจ สถาบันเทคโนโลยีไทย-ญี่ปุ่น (TNI) จัดทำ ‘Digital lean manufacturing coaching program’ ขึ้น เพื่อช่วยเหลือผู้ประกอบการปรับปรุงกระบวนการผลิตควบคู่ไปกับการพัฒนาบุคลากรอย่างยั่งยืน กระบวนการนี้ประกอบด้วย 7 ขั้นตอนหลัก ซึ่งขั้นตอนที่ 1 และ 2 ตัวแทนผู้เข้าร่วมกระบวนการจะต้องมีทั้งบุคลากรระดับปฏิบัติการภายในโรงงาน วิศวกรโรงงาน หัวหน้าฝ่ายผลิตและฝ่ายที่เกี่ยวข้อง ไปจนถึงเจ้าหน้าที่ระดับบริหารที่มีข้อมูลภาพรวมของธุรกิจ เพื่อให้ทุกคนสามารถแบ่งปันข้อมูลและปัญหาจากประสบการณ์การทำงานจริงร่วมกันได้ และร่วมเป็นผู้รับผิดชอบในการพัฒนาองค์กร
“ขั้นตอนแรกของการโคชชิง (coaching) คือ ‘การสำรวจปัญหา’ ขั้นตอนนี้จะให้ทุกคนร่วมกันเขียนปัญหาที่พบจากการทำงานของตัวเองหรือจากข้อมูลเชิงลึกที่ตัวเองทราบ ขั้นตอนที่สอง คือ ‘การจัดลำดับความสำคัญของปัญหา’ โดยนำข้อมูลปัญหาที่สำรวจพบมาจัดกลุ่ม พิจารณาความเชื่อมโยง และจัดลำดับความสำคัญของปัญหา เพราะในความเป็นจริงแล้วแต่ละองค์กรอาจแก้ปัญหาทั้งหมดพร้อมกันไม่ได้ ทั้งด้วยข้อติดขัดด้านงบประมาณและบุคลากร ขั้นตอนที่สาม คือ ‘การฝึกอบรมบุคลากร’ ในหัวข้อที่เกี่ยวข้องกับปัญหาที่กำลังแก้ไข ซึ่งในขั้นตอนนี้อาจใช้การจำลองทางคอมพิวเตอร์ (computer simulation) และเทสต์เบด (testbed) ที่ SMC มีให้บริการร่วมด้วย เพื่อให้เกิดผลสัมฤทธิ์ในการเรียนรู้มากที่สุด
“หลังจากบุคลากรมีความรู้และทักษะพื้นฐานที่เกี่ยวข้องกับการแก้ปัญหานั้น ๆ แล้ว ก็จะเข้าสู่ขั้นตอนที่สี่ คือ ‘การวิเคราะห์และพัฒนาแนวทางการแก้ปัญหา’ ซึ่งในที่นี้จะเป็นการร่วมกันวิเคราะห์กระบวนการทำงานที่ปฏิบัติอยู่ในปัจจุบันเพื่อระดมความคิดเกี่ยวกับวิธีแก้ปัญหาและร่วมออกแบบกระบวนการทำงานรูปแบบใหม่ รวมถึงพิจารณาเลือกใช้เทคโนโลยีที่เหมาะสมกับสถานการณ์เพื่อการลดความสูญเปล่าให้ได้มากที่สุด ขั้นตอนที่ห้า คือ ‘การวางแผนดำเนินงานแก้ปัญหา’ เพื่อกำหนดขั้นตอนการดำเนินกิจกรรม ผู้รับผิดชอบ ระยะเวลา และงบประมาณให้ชัดเจน ขั้นตอนที่หก คือ ‘การดำเนินงานตามแผนในลักษณะ on the job training (OJT)’ เพื่อเรียนรู้วิธีแก้ปัญหาในสถานการณ์จริง โดยมีผู้เชี่ยวชาญเป็นพี่เลี้ยงอย่างใกล้ชิด และขั้นตอนสุดท้าย คือ ‘การให้คำปรึกษาด้านการปรับปรุงและพัฒนาอย่างต่อเนื่อง’ เพื่อให้ผู้ประกอบการวางแผนการพัฒนาโรงงานได้อย่างเหมาะสม เท่าทันต่อสถานการณ์ และบุคลากรภายในองค์กรมีความรู้ ความเข้าใจ และความพร้อม สอดรับกับรูปแบบการทำงานอยู่เสมอ”
Low-cost Solution เทคโนโลยีราคาจับต้องได้โดยนักวิจัยไทย
เมื่อพูดถึงการปรับเปลี่ยนเทคโนโลยีภายในโรงงาน ผู้ประกอบการหลายคนอาจปฏิเสธทันที เพราะมีภาพจำว่าการลงทุนต้องเป็นหลักแสน หลักล้าน หรือหลักสิบล้านบาท เพราะบุคลากรภายในโรงงานไม่สามารถปรับเปลี่ยนเทคโนโลยีหรือฟังก์ชันของเทคโนโลยีที่มีอยู่ให้สอดรับกับสถานการณ์การผลิตที่เปลี่ยนแปลงได้ ทำให้ต้องว่าจ้างผู้เชี่ยวชาญจากภายนอกมาปรับฟังก์ชัน หรืออาจถึงขั้นต้องลงทุนซื้อเทคโนโลยีใหม่มาใช้แทน ด้วยความตระหนักถึงปัญหาที่ผู้ประกอบการต้องเผชิญ นักวิจัยจากเนคเทค สวทช. จึงได้พัฒนาเทคโนโลยีทางเลือกเพื่อช่วยเหลือผู้ประกอบการในการแก้ปัญหาความสูญเปล่าด้วยหลักคิด ‘ลงทุนต่ำ ใช้งานได้จริง’
ดร.ธนกร ยกตัวอย่างถึง 2 เทคโนโลยีที่นักวิจัยเนคเทค สวทช. กำลังพัฒนาและอยู่ระหว่างการทดสอบใช้งานจริง เทคโนโลยีแรก คือ ‘Lean Flow’ ซอฟต์แวร์สำหรับออกแบบและปรับปรุงแผนผังการจัดวางเครื่องจักรและอุปกรณ์ภายในโรงงาน โดยนำโปรแกรม Microsoft Visio มาพัฒนาต่อยอด ซอฟต์แวร์ Lean Flow มีจุดเด่น คือ ใช้สร้างแผนภาพและคำนวณระยะการเดินทางของวัสดุ คน หรืออุปกรณ์ขนย้ายวัสดุได้สะดวก วิเคราะห์ผลกระทบด้านระยะทางอันเกิดจากการปรับเปลี่ยนแผนผังได้อย่างรวดเร็ว ใช้สร้างแผนผังภายในโรงงานได้ครอบคลุมทั้งสายการผลิต ตั้งแต่ตำแหน่งที่นำวัตถุดิบเข้าโรงงาน ตำแหน่งของเครื่องจักรและอุปกรณ์ที่ใช้ในการผลิตและตรวจสอบคุณภาพสินค้า ไปจนถึงการจัดส่งสินค้าที่ผลิตเสร็จแล้วไปยังโกดัง ทำให้วิศวกรโรงงานทดลองสร้างแผนผังในรูปแบบต่าง ๆ และเลือกรูปแบบการทำงานที่มีประสิทธิภาพสูงสุดได้สะดวกและรวดเร็ว


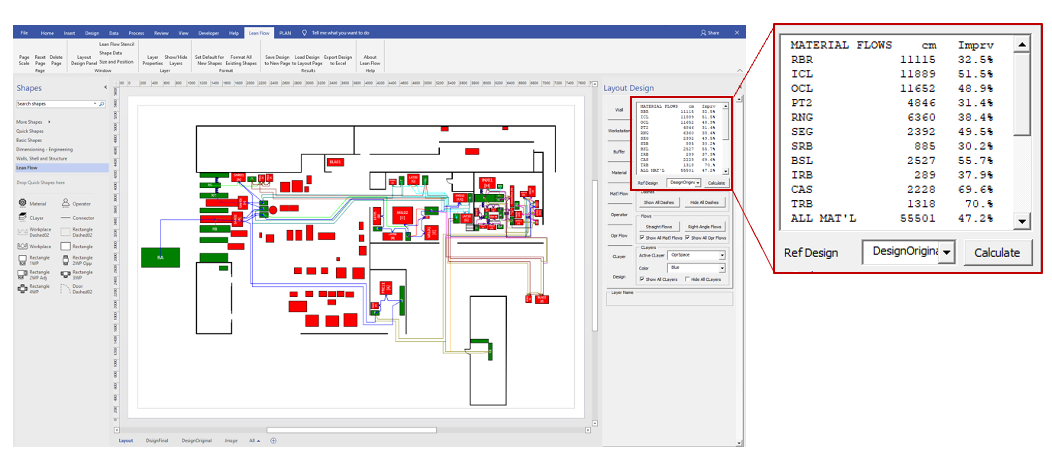
“เทคโนโลยีที่สอง คือ ‘Smart OEE’ หรือชุดเครื่องมือสำหรับติดตามประสิทธิผลโดยรวมของเครื่องจักร (overall equipment effectiveness: OEE) ที่ใช้ในการผลิตแบบเรียลไทม์ พร้อมจัดแสดงผลข้อมูลในรูปแบบชุดข้อมูลที่ทำความเข้าใจได้ง่าย โดยเครื่องมือประกอบด้วย ‘IoT (Internet of Things) gateway’ หรืออุปกรณ์สำหรับรับข้อมูลจากเครื่องจักรหรือเซนเซอร์ต่าง ๆ ภายในโรงงาน และ ‘ซอฟต์แวร์ Smart OEE’ ซึ่งเป็นซอฟต์แวร์สำหรับประมวลผลที่นำ Node-RED มาพัฒนาต่อยอด โดยวิศวกรโรงงานสามารถนำระบบ Smart OEE ไปใช้คำนวณค่า OEE ของเครื่องจักรต่าง ๆ ภายในโรงงาน เพื่อให้ผู้ประกอบการ และผู้วางแผนการผลิตเห็นถึงตัวเลขประสิทธิผลที่ชัดเจนและเป็นปัจจุบัน ทำให้วางแผนการทำงานหรือปรับปรุงกระบวนการทำงานได้อย่างมีประสิทธิภาพมากยิ่งขึ้น”


จากที่กล่าวมาข้างต้นจะเห็นได้ว่าการปรับปรุงโรงงานด้วยหลักคิด lean manufacturing ไม่จำเป็นต้องลงทุนสูงเสมอไป สิ่งสำคัญสุดคือการพิจารณาปัญหาและวางแผนการทำงานที่มุ่งเป้าและแม่นยำ เพื่อให้ทุกการลงทุนปรับเปลี่ยนเกิดประโยชน์สูงสุด
ดร.ธนกร อธิบายเพื่อสร้างความตระหนักทิ้งท้ายว่า แม้ lean manufacturing จะมีหลักการที่ตรงไปตรงมา รวมถึงที่ผ่านมานักวิจัยทั้งในประเทศไทยและต่างประเทศต่างช่วยกันพัฒนากระบวนการดำเนินงาน (protocol) และเทคโนโลยีสนับสนุนต่าง ๆ เพื่อให้การปฏิบัติตามหลัก lean manufacturing ทำได้ง่ายขึ้นมาก จนหลายคนอาจหลงคิดว่าการจะปรับเปลี่ยนโรงงานไม่จำเป็นต้องเรียนรู้อะไรเพิ่มเติมมาก ทำไม่นานก็จะเห็นผล แต่ในความเป็นจริงแล้วจนถึงปัจจุบันหากสืบค้นข้อมูลผ่านอินเทอร์เน็ตจะพบว่า ‘ในภาพรวมมีตัวเลขที่รายงานถึงความสำเร็จในการปรับปรุงโรงงานอย่างยั่งยืนตามหลัก lean manufacturing น้อยกว่าร้อยละ 50’ สาเหตุส่วนหนึ่งมาจากผู้บริหารขาดความรู้ความเข้าใจอย่างลึกซึ้ง จึงไม่สามารถผลักดันพนักงานภายในองค์กรให้มีส่วนร่วมดำเนินงานจนประสบความสำเร็จได้ และที่สำคัญอย่างยิ่งคือ ‘ขาดการทำอย่างต่อเนื่อง’ เพราะในระยะแรกของการนำระบบ lean manufacturing เข้าไปใช้ แต่ละองค์กรอาจปรับเปลี่ยนไม่สำเร็จในทันที หรือทำแล้วยังไม่เห็นผลการเปลี่ยนแปลงอย่างมีนัยสำคัญในเวลาอันสั้น ทำให้ล้มเลิกความตั้งใจไปเสียก่อน
“สิ่งที่หนึ่งที่ผู้ประกอบการ รวมถึงบุคลากรภายในองค์กรควรต้องตระหนักเป็นอย่างยิ่ง คือ lean manufacturing เป็นหลักการที่จะเห็นผลได้อย่างชัดเจนและยั่งยืนก็ต่อเมื่อคนภายในองค์กรช่วยกันปรับเปลี่ยนจนมีวัฒนธรรม Lean เป็นหลักคิดพื้นฐาน เปรียบเสมือนกับการปลูกต้นไม้ที่ต้องคอยดูแลเป็นพิเศษในช่วงเริ่มแรก จนต้นไม้แข็งแรงออกดอกออกผลอย่างยั่งยืนในระยะยาว”
สำหรับผู้ที่สนใจกระบวนการ lean manufacturing และเทคโนโลยีที่เกี่ยวข้อง สอบถามรายละเอียดเพิ่มเติมได้ที่ ศูนย์นวัตกรรมการผลิตยั่งยืน (SMC) สวทช. เว็บไซต์ www.nectec.or.th/smc/ เฟซบุ๊ก SMC อีเมล smc-business@nectec.or.th และ LINE @smceeci
เรียบเรียงโดย ภัทรา สัปปินันทน์ ฝ่ายสร้างสรรค์สื่อและผลิตภัณฑ์ สวทช.
อาร์ตเวิร์กโดย ภัทรา สัปปินันทน์
ภาพประกอบโดย ภัทรา สัปปินันทน์, เนคเทค สวทช. และ shutterstock